Using Computer Vision for Automated Assembly Line Inspection
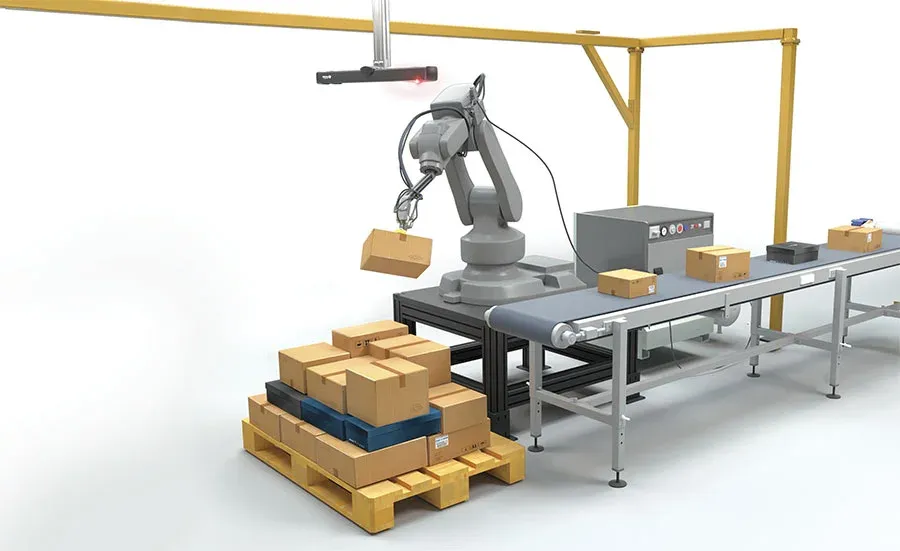
Table of Contents
- Introduction
- Role of Computer Vision in Automated Assembly Line Inspection
- Steps Involved in Computer Vision-Based Automated Assembly Line Inspection
- Enhancing Automated Assembly Line Inspection with Computer Vision
- Applications and Real-world Impact
- Challenges and Considerations
- Future Trends in Computer Vision for Automated Assembly Line Inspection
- Conclusion
- Frequently Asked Questions
Introduction
In the ever-evolving landscape of manufacturing, where precision and efficiency are paramount, the integration of computer vision into automated assembly line inspection represents a transformative leap forward. As industries strive to meet and exceed stringent quality standards, the role of computer vision becomes pivotal in reshaping traditional quality assurance practices.
This blog unfolds the intricate tapestry of how computer vision technologies are not merely augmenting but revolutionizing the way products are inspected on assembly lines.
From unparalleled precision in defect detection to real-time monitoring and adaptive responses, this exploration delves into the multifaceted dimensions that characterize the synergy between computer vision and automated assembly line inspection.
Join us on a journey through the intricacies of this technological marriage and its profound impact on the future of manufacturing quality assurance.
Role of Computer Vision in Automated Assembly Line Inspection
In the realm of automated assembly line inspection, the integration of computer vision emerges as a game-changer, ushering in unprecedented advancements in precision, efficiency, and adaptability.
At its core, computer vision refers to the utilization of artificial intelligence (AI) and image processing algorithms to enable machines to interpret and comprehend visual information.
In the context of assembly line inspection, this technology revolutionizes the way products are scrutinized, elevating quality assurance to new heights.
- Precision in Defect Detection:One of the primary contributions of computer vision is its unparalleled ability to detect defects with remarkable precision. Automated systems equipped with sophisticated algorithms can identify even the minutest deviations from quality standards, ensuring that products leaving the assembly line are free from imperfections.
- Speed and Efficiency:Computer vision accelerates the inspection process, outpacing traditional manual methods. With the capability to process visual data at exceptional speeds, automated systems equipped with computer vision technologies enhance the efficiency of assembly line inspections, enabling swift assessments without compromising accuracy.
- Multi-faceted Inspections:Unlike manual inspections that may be limited by human capacity, computer vision allows for multi-faceted inspections. These systems can simultaneously assess various quality parameters, such as defects, dimensions, and classifications, contributing to a comprehensive evaluation of products in a single streamlined process.
- Adaptability to Product Variations:Manufacturing often involves diverse product variations within the same assembly line. Computer vision systems exhibit a high degree of adaptability, capable of learning and recognizing different product characteristics. This adaptability ensures that the technology remains effective across a spectrum of products, accommodating variations in shape, size, and features.
- Reduction of Human Error:Automation through computer vision significantly reduces the inherent risks of human error in inspections. By replacing subjective human judgment with objective and consistent algorithms, the technology minimizes the chances of overlooking defects or introducing variability into the inspection process.
- Real-time Monitoring for Immediate Action:One of the defining features of computer vision in automated assembly line inspection is its real-time monitoring capabilities. The systems continuously analyze visual data, allowing for immediate identification of deviations or defects. This real-time feedback loop facilitates prompt corrective actions, preventing the production of substandard products and minimizing potential waste.
- Consistency in Quality Control:Ensuring consistency in quality control is a hallmark of computer vision applications. Automated inspections powered by computer vision maintain a uniform standard across all assessments, eliminating variations that may arise from human fatigue or subjective judgment. This consistency contributes to the reliability of the entire quality assurance process.
Steps Involved in Computer Vision-Based Automated Assembly Line Inspection
- Data Collection and Preprocessing:The process begins with the collection of visual data relevant to the assembly line. This data may include images or videos capturing different stages of the manufacturing process. Subsequently, preprocessing techniques are applied to refine and enhance the quality of the collected data, ensuring optimal conditions for subsequent analysis.
- Data Annotation:The annotated dataset is a cornerstone for training computer vision models. During this step, each image or frame in the dataset is labeled with specific information, such as defect locations, product classifications, or relevant features. Accurate annotation is critical for training tools like Labellerr to facilitate this process, ensuring accurate annotations for effective model training the model to recognize and interpret visual patterns.
- Model Selection and Architecture:Choosing the appropriate computer vision model is a pivotal decision. Depending on the complexity of the inspection task, different architectures such as convolutional neural networks (CNNs) or recurrent neural networks (RNNs) may be selected. The model's architecture is tailored to the specific requirements of the assembly line inspection.
- Model Training:With the annotated dataset and selected model, the training phase commences. During this step, the model learns to recognize patterns and features within the annotated data. The training process involves adjusting the model's parameters iteratively to optimize its ability to accurately classify, detect, or segment components within the visual data.
- Augmentation Techniques:To enhance the model's robustness and ability to generalize, augmentation techniques are applied. These techniques involve introducing variations in the training data, such as rotations, flips, or changes in lighting conditions. Augmentation helps the model adapt to different scenarios it may encounter during actual assembly line inspections.
- Validation and Testing:The trained model undergoes validation and testing phases to assess its performance. Validation involves evaluating the model on a separate dataset not used during training, ensuring it generalizes well to new data. Testing involves deploying the model in a controlled environment to assess its real-world applicability.
- Integration and Deployment:Once the model demonstrates satisfactory performance, it is integrated into the assembly line inspection system. This integration involves connecting the computer vision model with the hardware and software components of the assembly line. Deployment ensures that the model seamlessly becomes a part of the production process.
- Real-time Processing and Optimization:The final step focuses on real-time application and optimization. The computer vision system now operates in real-time, continuously analyzing visual data from the assembly line. Optimization processes may involve fine-tuning the model based on real-world performance, ensuring consistent and reliable inspection results.
Enhancing Automated Assembly Line Inspection with Computer Vision
The application of computer vision to automated assembly line inspection in manufacturing yields a number of revolutionary improvements. This section delves into the particular ways that computer vision technologies transform conventional quality assurance procedures by improving and elevating the inspection process.
- Improved Precision and Accuracy:Computer vision imparts an unprecedented level of precision and accuracy to assembly line inspections. By leveraging advanced algorithms and image processing techniques, the technology ensures the identification of defects with unparalleled accuracy, minimizing false positives and negatives.
- Seamless Integration with Existing Systems:The integration of computer vision seamlessly fits into existing manufacturing ecosystems. Compatibility with diverse hardware and software components ensures a smooth transition, allowing industries to harness the benefits of automated inspections without disrupting established processes.
- Increased Speed and Throughput:Automation through computer vision significantly accelerates the inspection process. With the ability to process visual data at high speeds, automated assembly line inspections outpace traditional manual methods. This increase in throughput contributes to enhanced overall efficiency in manufacturing.
- Real-time Monitoring for Adaptive Responses:Computer vision facilitates real-time monitoring of the assembly line. The system continuously analyzes visual data, enabling immediate responses to deviations or defects. This adaptive capability ensures swift corrective actions, preventing the production of substandard products and minimizing disruptions.
- Comprehensive Quality Control:The holistic nature of computer vision-based inspections allows for comprehensive quality control. Beyond defect detection, these systems can simultaneously assess various quality parameters, including dimensional accuracy, labeling, and packaging verification. This comprehensive approach ensures a thorough evaluation of every product.
- Cost Reduction and Resource Optimization:Automated assembly line inspections powered by computer vision contribute to cost reduction. By minimizing the need for extensive manual labor, industries can optimize resource utilization. The efficiency gains achieved through automation translate into economic viability and enhanced profitability.
Applications and Real-world Impact
The incorporation of computer vision into automated assembly line inspection transcends theoretical advancements, manifesting tangible benefits across a spectrum of applications. This section delves into real-world scenarios where computer vision technologies redefine quality assurance in manufacturing, showcasing their diverse applications and profound impact.
- Automated Defect Detection:
Application: Identifying and categorizing defects in manufactured products.
Impact: Swift and accurate detection ensures that only products meeting quality standards proceed down the assembly line, minimizing the production of faulty goods. - Product Classification and Sorting:
Application: Automated sorting of products based on predefined criteria.
Impact: Enables efficient categorization, ensuring each product is directed to the appropriate destination, streamlining production workflows. - Dimensional Accuracy Checks:
Application: Verifying product dimensions against predefined standards.
Impact: Ensures that products adhere to precise specifications, reducing variations in size and enhancing overall product quality. - Label and Packaging Verification:
Application: Automated validation of labels, barcodes, and packaging integrity.
Impact: Guarantees compliance with regulatory requirements, enhances product presentation, and mitigates the risk of mislabeled or damaged items. - Quality Control in Food and Pharmaceuticals:
Application: Stringent inspection for contaminants, irregularities, or deviations in sensitive industries.
Impact: Safeguards consumer health by ensuring the production of safe and high-quality products in sectors like food and pharmaceuticals. - Increased Manufacturing Efficiency:
Application: Streamlining production processes through automated inspections.
Impact: Enhances overall manufacturing efficiency by reducing the time required for manual inspections, optimizing workflow, and increasing throughput. - Supply Chain Traceability:
Application: Capturing and analyzing visual data throughout production and distribution.
Impact: Enhances transparency in the supply chain, facilitating tracking and identification of the source of quality issues.
Challenges and Considerations
While computer vision brings transformative benefits to automated assembly line inspection, its integration is not without challenges. Navigating these complexities is crucial for successful implementation.
This section explores the key challenges and considerations associated with leveraging computer vision in the realm of manufacturing quality assurance.
- Handling Product Variations:
Challenge: Diverse product shapes, sizes, and features may pose challenges in creating a one-size-fits-all computer vision model.
Consideration: Developing adaptive models capable of recognizing and accommodating variations within product lines, ensuring versatility in inspection capabilities. - Ambient Conditions and Lighting:
Challenge: Variations in lighting conditions across different shifts or production environments can impact the quality of visual data.
Consideration: Implement robust algorithms that can adapt to varying lighting conditions or integrate consistent lighting solutions within the inspection environment. - Data Quality and Annotation Challenges:
Challenge: Insufficient or inaccurately annotated data can hinder the model's ability to generalize effectively.
Consideration: Ensuring high-quality, diverse datasets for training, and implementing rigorous annotation processes to enhance model accuracy. - Integration Complexity:
Challenge: Integrating computer vision into existing manufacturing systems may present technical challenges and require compatibility adjustments.
Consideration: Conducting thorough system audits, collaborating with IT specialists, and selecting integration approaches that minimize disruptions to ongoing operations. - Scalability and Performance:
Challenge: As production volumes increase, the performance of computer vision systems may face scalability challenges.
Consideration: Designing systems with scalability in mind, employing parallel processing, and utilizing hardware accelerators to maintain optimal performance under increased workloads. - Ethical and Regulatory Compliance:
Challenge: Adhering to ethical standards and compliance with industry-specific regulations is paramount, especially in sensitive industries.
Consideration: Establishing clear ethical guidelines for the use of computer vision, ensuring data privacy, and staying abreast of industry-specific regulations to avoid legal ramifications. - Human-AI Collaboration:
Challenge: Striking the right balance between automated systems and human oversight is critical for effective quality control.
Consideration: Defining clear protocols for collaboration, ensuring effective communication between automated systems and human inspectors, and leveraging the strengths of both for optimal results.
Future Trends in Computer Vision for Automated Assembly Line Inspection
As technology continues to advance, the future of computer vision in automated assembly line inspection holds exciting possibilities. Anticipated trends point towards further refinement, efficiency, and adaptability, ensuring that quality assurance processes evolve to meet the demands of an ever-changing manufacturing landscape.
- Advancements in Deep Learning Architectures:
Trend: Continued evolution of deep learning architectures for enhanced pattern recognition and feature extraction.
Impact: Improved model accuracy, enabling more nuanced defect detection and classification, especially in complex manufacturing scenarios. - Edge Computing for Real-time Processing:
Trend: Increased reliance on edge computing to process visual data in real-time directly at the source.
Impact: Reduced latency, enabling faster decision-making and immediate corrective actions on the assembly line, enhancing overall operational efficiency. - Explainable AI for Enhanced Transparency:
Trend: Growing emphasis on explainable AI, allowing users to understand and interpret the decision-making processes of computer vision models.
Impact: Increased trust in automated inspection systems, easier identification of potential biases, and compliance with regulatory requirements. - Multi-modal Sensing Integration:
Trend: Integration of data from multiple sensing modalities (e.g., visual, thermal, or infrared sensors) for more comprehensive inspections.
Impact: Enhanced detection capabilities, especially in challenging environments where visual data alone may be insufficient. - Continuous Learning and Adaptability:
Trend: Implementation of continuous learning models that adapt to evolving production environments.
Impact: Increased adaptability, allowing the system to learn from new data and adjust to changes in manufacturing processes over time. - AI-driven Automated Annotation:
Trend: Automation of the data annotation process using AI algorithms.
Impact: Accelerated model training, reduced reliance on manual annotation, and improved scalability for large and diverse datasets. - Increased Collaboration Across Industries:
Trend: Greater collaboration between industries to share knowledge and best practices in computer vision applications.
Impact: Accelerated development and adoption of advanced inspection technologies, leveraging insights from diverse manufacturing sectors.
Conclusion
The integration of computer vision into automated assembly line inspection heralds a new era in manufacturing quality assurance. The precision, speed, and adaptability offered by computer vision redefine the standards of product quality, ensuring industries stay at the forefront of technological advancements.
As we navigate the challenges and embrace future trends, the symbiotic relationship between computer vision and automated assembly line inspection promises a future where quality assurance is synonymous with efficiency and innovation.
Frequently Asked Questions
Q1.How is machine vision useful in automated inspection?
Automated inspection benefits greatly from machine vision since it gives machines the ability to analyze and comprehend visual data from pictures or videos. It is employed in manufacturing to detect deviations from intended norms in order to ensure uniformity in product assembly, control quality, and discover defects.
Q2.How computer vision is changing manufacturing in 2023?
A transformation has seen in 2023 in manufacturing thanks to computer vision, which will increase automation, efficiency, and precision. It is used for process optimization, predictive maintenance, and real-time quality assurance. Cutting-edge computer vision technologies are increasing productivity overall, decreasing errors, and optimizing production processes.
Q3.What is computer vision in automation?
The integration of visual perception capabilities into automated systems is known as computer vision in automation. It entails giving machines the ability to understand and react to visual input by utilizing cameras, image processing, and machine learning algorithms. This technology is essential for jobs like item detection, quality control, and robot navigation in manufacturing because it improves the accuracy and efficiency of automated processes.
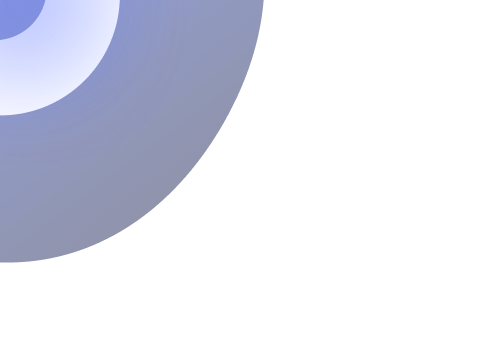
Simplify Your Data Annotation Workflow With Proven Strategies
.png)
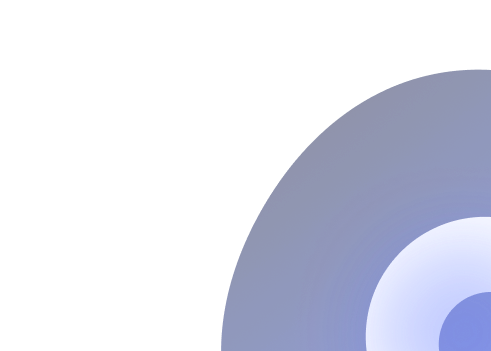