Transforming Industrial Maintenance With Computer Vision
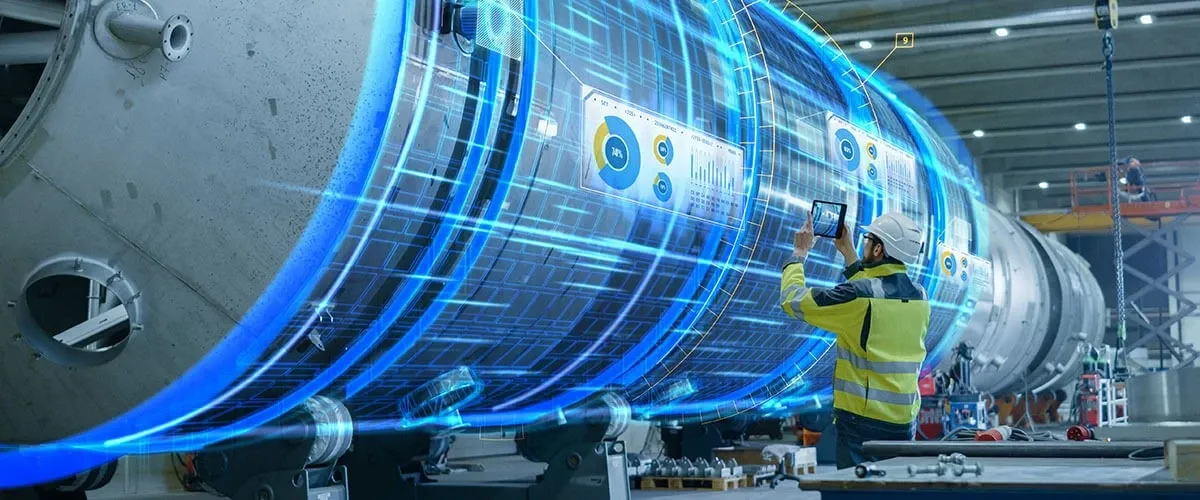
Table of Contents
- Introduction
- Computer Vision Transforming Equipment Health Monitoring
- Model Implementation
- Challenges
- Conclusion
- Frequently Asked Questions
Introduction
There was a busy factory where machines was working day and night to produce goods. But there was a major issue: the devices frequently stopped working suddenly.
This generated a lot of difficulties for both the workers and the industrial managers.
Did you know? Many factories confront the same issue.
According to studies, these sudden interruptions cost a lot of money—nearly $260,000 for every hour the machines are down!
Then one day, the plant owners learned about something called "computer vision".
It's a smart technology that utilises cameras and computers to examine objects and identify faults. They reasoned, "Maybe this could help us!"
So they decided to test it out. They installed cameras throughout the factory to monitor the machinery closely.
When something seemed incorrect, the cameras would alert the personnel immediately.
And, guess what? It works.
Workers can use computer vision to solve problems before they become major issues.
The machines began to work more efficiently, and the factory became a happier environment.
The employers were also pleased since they had saved a significant amount of money.
With computer vision, the production experienced fewer unplanned stoppage, allowing everyone to work more efficiently.
This is one such scenario. Let's go further to learn how computer vision is changing equipment health monitoring.
Computer Vision Transforming Equipment Health Monitoring
Computer vision has emerged as a powerful tool in equipment health monitoring, revolutionizing the way industries ensure the optimal performance and reliability of their machinery. Here's how computer vision is making a difference:
1.Visual Inspection:
- Traditional methods of equipment monitoring often rely on manual inspections, which can be time-consuming and prone to human error.
- Computer vision automates this process by analyzing images or video feeds from cameras installed on or near the equipment.
- This allows for continuous monitoring and immediate detection of abnormalities or defects.
2.Defect Detection:
- Computer vision algorithms can be trained to identify specific defects or anomalies in machinery components.
- Whether it's cracks, corrosion, leaks, or misalignments, computer vision systems can pinpoint issues that may indicate potential failures.
- By detecting defects early, maintenance teams can take proactive measures to prevent downtime and costly repairs.
3.Condition Monitoring:
- Through continuous analysis of visual data, computer vision systems can assess the condition and performance of equipment in real-time.
- By monitoring factors such as temperature, vibration, and wear patterns, these systems can provide insights into the health of machinery and predict potential failures before they occur.
4.Remote Monitoring:
- Computer vision enables remote monitoring of equipment health, allowing operators and maintenance personnel to access real-time visual data from anywhere with an internet connection.
- This flexibility facilitates proactive maintenance and troubleshooting, even for equipment located in remote or hazardous environments.
5.Predictive Maintenance:
- By combining computer vision with predictive analytics, organizations can move from reactive to proactive maintenance strategies.
- By analyzing historical data and identifying patterns of equipment degradation, predictive maintenance models can anticipate maintenance needs and schedule interventions at optimal times, minimizing downtime and maximizing productivity.
6.Integration with IoT and AI:
- Computer vision is often integrated with other technologies such as the Internet of Things (IoT) and artificial intelligence (AI). IoT sensors collect data from equipment, while AI algorithms analyze this data alongside visual inputs from computer vision systems. This integration enables comprehensive monitoring and analysis of equipment health, leading to more informed decision-making and optimized maintenance strategies.
7.Enhanced Safety:
- In addition to monitoring equipment health, computer vision can also contribute to workplace safety by detecting unsafe conditions or behaviors. For example, computer vision systems can identify personnel operating machinery without proper safety gear or alert operators to potential hazards in the workspace.
In summary, computer vision is transforming equipment health monitoring by providing real-time insights, enabling predictive maintenance, and enhancing safety in industrial environments.
As technology continues to evolve, the role of computer vision in equipment monitoring will only become more critical in ensuring the reliability, efficiency, and safety of industrial operations.
Model Implementation
Let's consider the scenario of monitoring industrial pumps in a manufacturing facility using computer vision for equipment health monitoring.
Here's how we can implement it in more detail:
1. Data Collection:
Install cameras or sensors near the industrial pumps to capture visual data, including images or videos of the pump's operation.
Collect data under various operating conditions, including normal operation, start-up, shutdown, and during maintenance activities.
2. Annotation:
Annotate the collected data to label different states of the pump, such as normal operation, abnormal operation (e.g., leaks, vibrations), and maintenance activities.
Use annotations to provide context for training the machine learning model and identifying patterns associated with equipment health.
Employ expert annotations for complex tasks(like Labellerr etc).
3. Data Preprocessing:
Preprocess the collected data to extract relevant features from the images or video frames.
Apply techniques such as image cropping, resizing, and normalization to standardize the input data for model training.
Consider additional preprocessing steps such as denoising or contrast enhancement to improve the quality of the input data.
4. Model Development:
Choose a suitable machine learning algorithm for equipment health monitoring, such as Convolutional Neural Networks (CNNs) or Recurrent Neural Networks (RNNs) for sequence data.
Design the architecture of the model to process the preprocessed data and predict the state of the industrial pump based on the visual input.
Train the model using the annotated dataset, optimizing model parameters to achieve accurate predictions of equipment health states.
5. Integration with Equipment Monitoring System:
Integrate the trained machine learning model with the equipment monitoring system to analyze real-time visual data from the industrial pumps.
Develop software interfaces to capture and preprocess images or video streams from the cameras installed near the pumps.
Implement mechanisms to perform inference using the trained model and classify the current state of the pump (e.g., normal, abnormal, maintenance).
6. Real-time Monitoring and Alerting:
Create a monitoring dashboard or user interface to visualize the current state of the industrial pumps and track changes over time.
Set up alerting mechanisms to notify operators or maintenance personnel when abnormal conditions are detected, indicating potential equipment failures or maintenance requirements.
7. Maintenance Workflow Integration:
Integrate the equipment health monitoring system with the facility's maintenance management system to streamline maintenance workflows.
Automatically generate work orders or maintenance tickets based on the detected equipment health states and prioritize maintenance tasks accordingly.
8. Continuous Improvement and Training:
Continuously monitor the performance of the equipment health monitoring system and collect feedback from operators and maintenance personnel.
Periodically retrain the machine learning model using updated data to adapt to changes in equipment behavior or environmental conditions.
Evaluate the effectiveness of the model updates and refine the monitoring system to improve accuracy and reliability over time.
Challenges
Implementing computer vision-based equipment health monitoring systems for industrial applications presents several challenges:
Data Quality and Variability:
- Obtaining high-quality data for training and validation can be challenging due to variations in lighting conditions, camera angles, and environmental factors.
- Ensuring consistency and accuracy in data annotation is crucial but can be time-consuming and labor-intensive.
Anomaly Detection:
- Identifying anomalies or deviations from normal equipment behavior requires robust algorithms capable of distinguishing between normal variations and potential failure modes.
- Handling rare or novel anomalies that may not be well-represented in the training data poses additional challenges.
Model Generalization:
- Developing machine learning models that generalize well across different equipment types, operating conditions, and environmental settings is essential for deploying monitoring systems in diverse industrial environments.
- Ensuring the model's adaptability to changes in equipment behavior and performance over time is a continuous challenge.
Real-time Processing and Latency:
- Processing visual data in real-time and making timely decisions based on the analysis poses computational challenges, especially for high-resolution images or video streams.
- Minimizing inference latency is critical for enabling timely response to equipment failures or anomalies.
Scalability and Deployment:
- Deploying computer vision systems across large-scale industrial facilities requires scalable architectures capable of handling high volumes of visual data from multiple sensors and cameras.
- Ensuring seamless integration with existing equipment monitoring infrastructure and operational workflows is essential for successful deployment.
Robustness to Environmental Factors:
- Industrial environments are often characterized by harsh conditions, including dust, vibrations, and temperature fluctuations, which can affect the performance of camera systems and degrade the quality of visual data.
- Developing algorithms that are robust to environmental noise and artifacts is crucial for reliable equipment health monitoring.
Interpretability and Trustworthiness:
- Providing interpretable explanations for the model's decisions is important for building trust among operators and maintenance personnel.
- Ensuring transparency and accountability in the monitoring system's predictions helps facilitate effective decision-making and intervention strategies.
Data Privacy and Security:
- Protecting sensitive data collected by equipment monitoring systems from unauthorized access, tampering, or misuse is a significant concern.
- Implementing robust data encryption, access controls, and audit trails is essential for safeguarding data privacy and maintaining system integrity.
Addressing these challenges requires a multidisciplinary approach, combining expertise in computer vision, machine learning, data engineering, and domain-specific knowledge of industrial processes.
By overcoming these challenges, organizations can unlock the full potential of computer vision-based equipment health monitoring systems to enhance operational efficiency, reduce downtime, and improve overall equipment reliability.
Conclusion
In conclusion, computer vision is poised to revolutionize equipment health monitoring in industrial settings by providing real-time insights and predictive capabilities.
Despite challenges in data quality, model accuracy, and deployment scalability, the benefits of proactive maintenance and operational efficiency outweigh the obstacles.
By leveraging advanced machine learning algorithms and integrating with existing infrastructure, organizations can enhance equipment reliability, minimize downtime, and optimize maintenance workflows.
With ongoing innovation and collaboration across disciplines, computer vision holds the key to unlocking new levels of efficiency and reliability in industrial equipment monitoring, shaping the future of manufacturing and maintenance practices.
Frequently Asked Questions
Q1.How is computer vision used in manufacturing?
Computer vision is used in manufacturing for quality control, defect detection, object recognition, equipment monitoring, and process optimization.
Q2.What is computer vision platform for manufacturing?
A computer vision platform for manufacturing is a software solution that utilizes machine learning algorithms and image processing techniques to analyze visual data from manufacturing processes. It enables tasks such as defect detection, quality inspection, and predictive maintenance.
Q3.What are the uses of computer in manufacturing?
Computers in manufacturing are used for process automation, inventory management, supply chain optimization, production scheduling, quality control, equipment monitoring, and data analysis. They help improve efficiency, reduce costs, and enhance overall productivity in manufacturing operations.
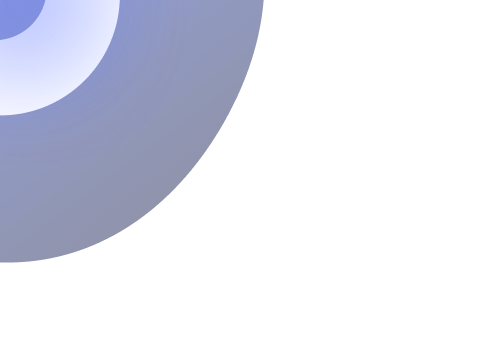
Simplify Your Data Annotation Workflow With Proven Strategies
.png)
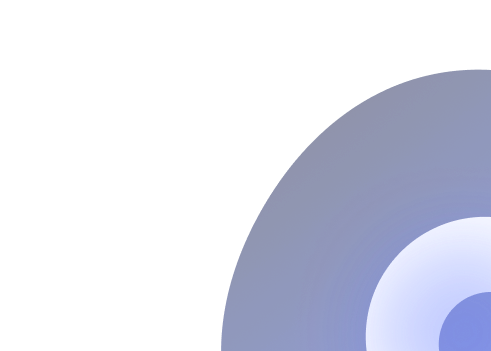