Bringing Computer Vision AI In Sawmill Industry
Root detection on logs in sawmill production ensures efficient operations by identifying defects, reducing waste, and enhancing timber quality and profitability.
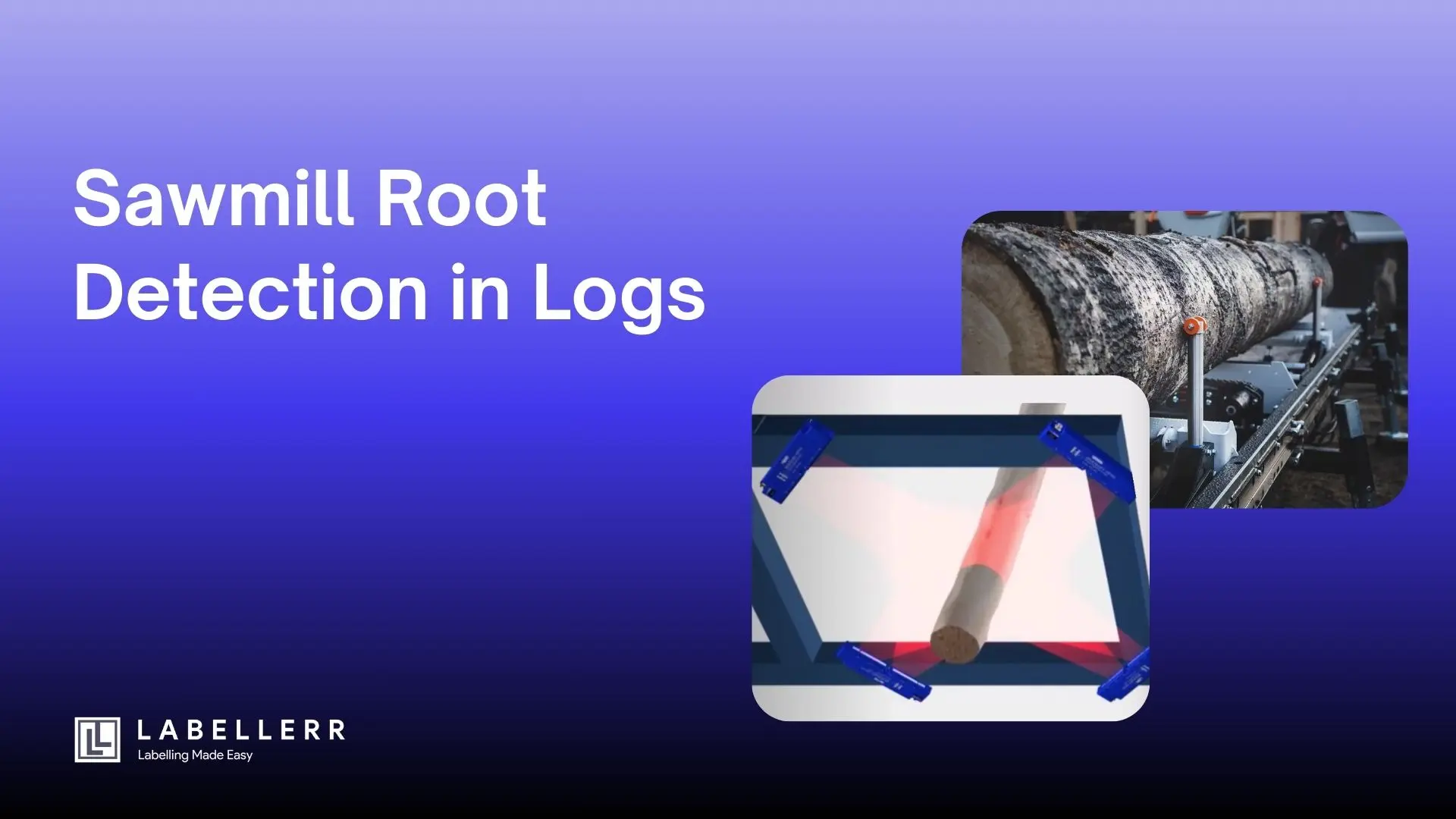
The industry of sawmill production requires efficiency. Each log processed needs to maximize wood quality, minimize waste, and avoid costly disruptions.
One hidden problem can cause big trouble: logs that still have roots attached. If a log enters the cutting machines with roots, it can cause damage, slow down operations, and lead to lower-quality timber.
Up to 24% of hardwood logs contain internal defects like knots, significantly reducing the yield of valuable timber.
For sawmill operators and timber industry professionals, addressing these hidden flaws is crucial to maximizing product value and optimizing production processes.
So, how do sawmills prevent this? By using AI-powered root detection!
In this blog, we'll take a closer look at how AI can automate the root detection process, the challenges sawmills face, and the benefits that this technology brings to the table.
Why Root Detection Matters
To process logs, workers first clean and debark them. The debarking process plays a crucial role by removing bark to prepare logs for cutting. However, roots attached to logs can jam or damage cutting machinery, lower efficiency, and produce low-grade wood.
Roots often create unevenness at the base of logs, making it essential to identify and remove these logs before processing to ensure a smooth production line. Traditionally, workers have performed this task manually, but this method has limitations, including human error, fatigue, and inefficiency.
The AI-Powered Solution: How It Works
Imagine a production line where cameras scan every log, and an AI model instantly detects the presence of roots. When the AI identifies roots, the system redirects the log for further processing before it continues down the line.
This solution uses computer vision and machine learning to create a seamless workflow, reduce downtime, and boost overall efficiency.
Here’s a simplified breakdown of the process:
- Logs enter the production line.
- Cameras or sensors scan each log.
- AI detects whether roots are present.
- Redirect logs with Roots for root removal.
- Clean logs continue to the next step, like debarking.
Challenges in Solving This Use Case
1. Complexity of Root Detection
- Variability in appearance: Roots may vary in size, color, and texture, making it difficult for a model to generalize across different logs.
- Dirty Surfaces: Logs may have dirt, bark, and other irregularities, which could lead to false positives or missed detections.
- Partial Roots: Some roots may be small or embedded, making them hard to detect without specialized models.
2. Real-Time Detection Requirements
- Speed vs. Accuracy: The AI model needs to operate in real time without delaying the production line, which requires optimizing both inference time and accuracy.
- Handling Large Volumes: A sawmill processes thousands of logs daily, so the detection system must handle high throughput efficiently.
3. Environmental Conditions
- Lighting Variability: Changes in lighting (e.g., outdoor vs. indoor) can affect camera input, making it challenging for the model to maintain accuracy.
- Dust and Noise Interference: Industrial environments often have dust, vibrations, and noise that could affect sensors or cameras.
4. Model Training and Fine-tuning
- Dataset Limitations: Collecting and annotating datasets of logs with roots is time-consuming, and models might require further fine-tuning for different wood types or regions.
- Model Generalization: The model must perform well across diverse environmental conditions without frequent retraining.
Solution: AI-powered detection
1. Data Collection
- Objective: Gather images of logs with and without roots to build a robust dataset.
- Use high-resolution cameras positioned along the production line to capture images from various angles.
- Ensure diverse lighting conditions and backgrounds to reflect real-world scenarios.
2. Data Annotation
- Objective: Label the collected images to identify the presence of roots.
- Utilize COCO (Common Objects in Context) format for annotation, marking bounding boxes or segmentation masks around the roots.
- Tools like Labellerr can be used for efficient labeling.
3. Data Preprocessing
- Objective: Prepare the annotated data for model training.
- Apply image augmentation techniques such as:
- Rotation: Rotate images to help the model recognize roots from different angles.
- Scaling: Resize images to different resolutions.
- Brightness Adjustment: Alter brightness levels to accommodate varying lighting conditions in the sawmill.
- Noise Addition: Introduce random noise to improve model robustness against environmental interferences.
4. Model Selection
- Objective: Choose a suitable architecture for root detection.
- Opt for a pre-trained model like YOLO (You Only Look Once) for object detection tasks.
- These models are chosen due to their ability to handle complex shapes and variations, providing a good starting point.
5. Model Training
- Objective: Fine-tune the selected model on the annotated dataset.
- Split the dataset into training, validation, and test sets (commonly in a 70-20-10 ratio).
- Hyperparameters:
- Set learning rate, batch size, and number of epochs. For example:
- Learning Rate: Start with 0.001 and adjust based on performance.
- Batch Size: Typically between 16 to 32 for a balanced training speed and memory usage.
- Number of Epochs: 50-100, depending on the dataset size and model convergence.
- Set learning rate, batch size, and number of epochs. For example:
- Use a loss function suitable for object detection,such as Binary Cross-Entropy for classifying whether roots are present.
- Monitor performance metrics like Intersection over Union (IoU) and mean Average Precision (mAP) during training.
6. Model Evaluation
- Objective: Assess the trained model's accuracy and robustness.
- Evaluate the model on the validation dataset to avoid overfitting.
- Analyze confusion matrices to understand detection performance and adjust model parameters if needed
7. Deployment
- Objective: Integrate the trained model into the sawmill’s production line.
- Deploy the model on edge devices (e.g., industrial computers) connected to cameras.
- Set up a real-time inference pipeline to process incoming log images and redirect logs with roots accordingly
Why AI is a Game-Changer for Sawmills
- Improved Efficiency: Streamlines the production process by quickly identifying and removing logs with roots, minimizing delays.
- Enhanced Wood Quality: Ensures only high-quality logs without defects are processed, leading to better end products.
- Cost Savings: Reduces waste and resource expenditure by preventing the processing of problematic logs.
- Increased Safety: Minimizes risks associated with handling irregular logs that could pose hazards during processing.
- Sustainability: Promotes responsible resource use by maximizing the yield from each log and reducing environmental impact.
Conclusion
AI-powered root detection is transforming the sawmill industry. With its ability to handle the complexities of real-world production environments, this technology reduces waste, improves safety, and enhances overall productivity.
Sawmills adopting these advancements are not only future-proofing their operations but also positioning themselves as leaders in sustainable wood processing.
This end-to-end solution not only addresses the challenges faced by sawmills but also lays the foundation for further process automation in the wood processing industry.
FAQs
- What is root detection in sawmill production?
Root detection is the process of identifying roots and internal defects in logs before processing. This ensures smooth operations, minimizes equipment damage, and improves the quality of the final timber product. - Why is root detection essential in sawmill production?
Root detection prevents defective logs from entering the production line, reducing equipment downtime, minimizing waste, and ensuring higher quality timber. It also helps optimize the cutting process for maximum efficiency. - How does root detection improve sawmill efficiency?
By identifying defects early, root detection allows sawmills to process logs more effectively, reducing machine wear and avoiding jams. This leads to streamlined workflows and increased productivity. - What are the challenges of manual root detection?
Manual root detection is prone to errors, inefficiency, and worker fatigue. These limitations can result in missed defects, lower productivity, and higher operational costs. - How does automated root detection benefit sawmill production?
Automated root detection uses advanced technologies to identify defects with high accuracy. This reduces reliance on manual inspection, improves consistency, enhances timber quality, and boosts profitability.
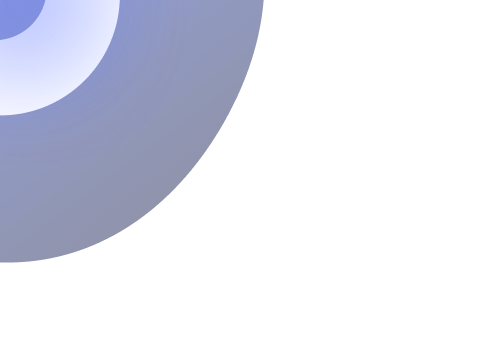
Simplify Your Data Annotation Workflow With Proven Strategies
.png)
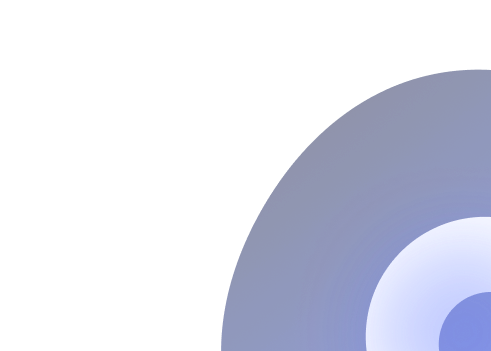